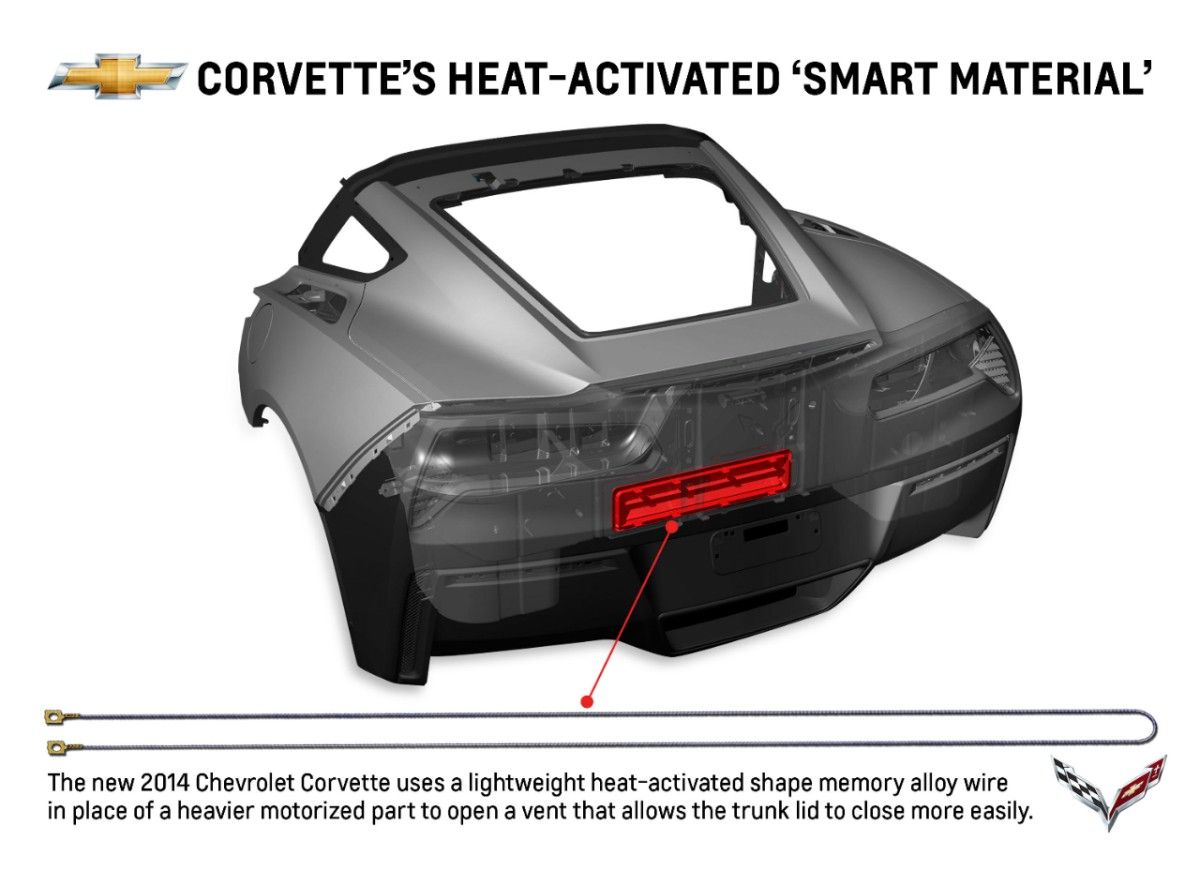
Savoir fabriquer un objet, c’est bien. Le rendre plus léger, plus performant et moins gourmand en énergie, c’est encore mieux ! C’est ce que recherchent les professionnels des industries technologiques en faisant appel à de nouveaux matériaux, ou en trouvant de nouvelles formules pour utiliser autrement des matériaux ou des alliages déjà connus.
La réalité est parfois encore plus excitante que la science-fiction. Grâce aux nanomatériaux, ces matériaux sous forme de suspension liquide, gel ou poudre invisibles à l’œil nu, on peut désormais fabriquer des composants minuscules. Les spécialistes des industries technologiques ne cessent de plancher sur de nouveaux matériaux, pour améliorer notre quotidien ou fabriquer des objets et moyens de locomotion encore plus performants. Comme les alliages à mémoire de forme, grâce auxquels un objet ou un composant peut subir de fortes tensions, être tordu dans tous les sens… et malgré tout retrouver sa forme initiale ! Ces alliages ont notamment été utilisés dans la prestigieuse Corvette, où un fil d’aluminium-nickel ou de nickel-titane a permis de remplacer un petit clapet motorisé : avec la mémoire de forme, plus besoin du petit moteur pour fermer le volet.
Mais les matériaux plus anciens n’ont pas à rougir pour autant devant ces petits nouveaux. Car certains, utilisés depuis des siècles, ont évolué avec les technologies et les produits. Le groupe Aperam, (une des sociétés fondatrices du RNM) fabrique des aciers inoxydables, notamment des alliages à base de nickel. Ces derniers sont utilisés dans l’industrie automobile et aéronautique pour leurs propriétés magnétiques afin de fabriquer des blindages électromagnétiques, des pièces électriques, des transformateurs… Mais pas seulement !
« Nous produisons des alliages pour répondre à des besoins de marchés, c’est ce qui fait évoluer nos produits », explique le responsable de la division alliages et aciers du groupe Aperam, Frédéric Mattei. Et depuis plusieurs années, la tendance est à l’allègement des voitures, des avions… pour leur faire consommer moins de carburant. L’entreprise a créé des alliages qui, à propriétés techniques identiques, nécessitent la mise en oeuvre de moins de matière première. Objectif : fabriquer les moteurs les plus petits possible, notamment ceux qui servent à incliner les fauteuils des avions. Ils sont étudiés en laboratoire par des experts en métallurgie puis fabriqués dans de grands fours de fusion.
Ces alliages semblent promis à un bel avenir puisque les secteurs de l’aéronautique et de l’automobile sont toujours en demande de nouvelles solutions plus performantes, capables de résister à de fortes chaleurs ou à des températures très basses, par exemple.
Les fabricants d’alliages ne sont pas les seuls à faire évoluer leurs produits pour répondre à de nouvelles demandes. On trouve la même tendance du côté du silicium, fabriqué à base de quartz dans de grands fours d’électrométallurgie. Ce métalloïde sert dans les applications chimiques, comme le silicone. On le trouve aussi dans des alliages, avec l’aluminium notamment, pour renforcer sa résistance (jantes de voitures notamment). « C’est l’inventivité des utilisateurs de nos produits qui guide nos développements », explique Bernard Plasse, président de la FNIEEC (fédération nationale des industries électrométallurgiques, électrochimiques et connexes) et membre d’A3M.
En effet, régulièrement, de nouvelles applications à base de silicium apparaissent. Il y a dix ans, dans quel contenant faisiez-vous un gâteau ? Sûrement pas dans un moule en silicone. Mais depuis une dizaine d’années, les ventes de ce produit ont explosé ! » explique-t-il.
Les panneaux photovoltaïques sont un autre exemple d’utilisation du silicium. L’un des enjeux actuels pour les acteurs du silicium est d’améliorer son efficacité. « Nous voulons augmenter le rendement de la cellule photovoltaïque, afin que toute la lumière du soleil arrivant dessus soit convertie en électricité », indique Bernard Plasse. Il s’agit donc de trouver les procédés capables d’optimiser le silicium qui sera ensuite transformé en cellules photovoltaïques. Une idée lumineuse, à l’heure où les industriels et les consommateurs cherchent à produire de l’électricité en limitant au maximum leurs émissions de CO2.
Pascale Raimbault ©2014 Les Industries Technologiques